Производственный процесс: Как делают платы для электроники H&F съездил в Подмосковье, чтобы узнать, как собирают электронику.
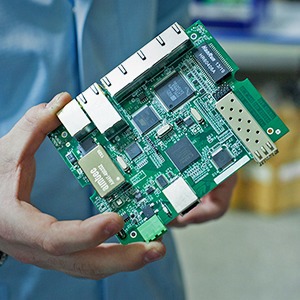
Производство плат расположилось на бывшем советском заводе, его территория до сих пор — режимный объект, поэтому H&F попросили не указывать ни название, ни адрес производства. Сборка плат для проекта «Мастер осанки» и самого устройства проходит в небольшом трёхэтажном строении, расположенном на огромной территории завода. Зимой кругом по колено снега, расчищены только дорожки, ведущие от здания к зданию, а летом сотрудники гуляют в сосновом бору и устраивают пикники на берегу озера, кишащего карпами, — небольшой лесопарк также находится в черте периметра. Здесь собирают и другую электронику. Иногда заказчиками выступают оборонные предприятия, а также автоконцерны.
Заказ поступает к менеджерам, которые должны запросить у заказчика комплект конструкторской документации, оценить сложность и возможности производства. На производство поступают документы и элементы, из которых будут собраны будущие платы. На первом этапе несколько инженеров сверяют все данные, проверяют соответствие информации в накладных. Предприятие работает в основном на давальческих комплектующих, но также ведёт и свою закупку. После проверки согласованная конструкторская документация поступает к операторам, чьи компьютеры подключены к единой производственной базе. Они ведут учёт и заполняют сопроводительные элементы.
Дальше элементы ставятся в порядке нанесения паяльной пасты на плату. Начальник смены либо старший по цеху знает, какое изделие идёт в плане, ставит нужный трафарет. Всё это приходит к операторам, они подготовливают программу для машины-конвейера, куда загружаются пустые печатные платы (зелёные) и которая подаёт их в принтер для нанесения. Чёрный крест на плате означает «битый блок» — брак производства. Аппарат камерой проверяет правильность установки, наносит пасту, и плата дальше по конвейеру уходит на визуальный осмотр.
На визуальном осмотре оператор проверяет качество нанесения. Плата выглядит уже иначе. На контактные площадки нанесена матовая паста, на них будут устанавливаться рабочие элементы машины. Паспортная производительность этой линии, состоящей из трёх станков, — 45 000 элементов в час. В реальности этот показатель немного ниже. В задачи оператора помимо первичной настройки входит заряжение питателя катушками с элементами. Тут две четырёхшпиндельные головки, которыми машина собирает плату. Часть элементов устанавливается вручную (если они пришли россыпью, а не в катушке, — тогда их не может взять автомат). Цена ручной работы выше, а качество — ниже, ведь человеческий фактор снижает повторяемость — показатель, важный на подобных производствах.
Дальше изделие уходит в двенадцатизонную печь. В ней десять нагревальных камер и две холодильные. Температурный профиль зависит от платы. Припой, так же как и паста, нуждаются в застывании. Температура плавления олова — 260°С, но в печи температура может быть выше или ниже. Из печи плата выгружается на конвейер.
Изделие уже собрано. Теперь оно должно пройти проверку. Для этого оно поступает к инженерам, которые ранее готовили техническую документацию и знают, что и как должно выглядеть и работать. Автоматически-оптическая инспекция включает в себя проверку правильности установки, правильность нанесения пасты, угол смещения элемента. Здесь выявляют брак и отправляют на доработку часть изделий. Сначала проблемные места выявляет машина. Ремонтная станция находится в том же отсеке, она редко используется, так как предназначена для ремонта крупных элементов. Ручной контроль осуществляют сотрудницы предприятия после автоматического контроля. Здесь ведётся статистика брака.
Выводной монтаж — здесь вручную устанавливают некоторые элементы с помощью паяльника. Некоторые платы нужно разрезать, для этого тоже есть специальная установка. К этому этапу плата снова изменилась. Она практически готова.
Пайка происходит с активными веществами, которые нужно смывать. Это разная неактивная химия. Чтобы отмыть платы, их помещают в камеры, очень похожие на обычные бытовые посудомоечные машины.
Этажом выше идёт процесс программирования, фокусирования, проверки и упаковки «Мастера осанки» в блистеры.
Фотографии: Лена Цибизова
Чтобы прочитать целиком, купите подписку. Она открывает сразу три издания
месяц
год
Подписка предоставлена Redefine.media. Её можно оплатить российской или иностранной картой. Продлевается автоматически. Вы сможете отписаться в любой момент.
На связи The Village, это платный журнал. Чтобы читать нас, нужна подписка. Купите её, чтобы мы продолжали рассказывать вам эксклюзивные истории. Это не дороже, чем сходить в барбершоп.
The Village — это журнал о городах и жизни вопреки: про искусство, уличную политику, преодоление, травмы, протесты, панк и смелость оставаться собой. Получайте регулярные дайджесты The Village по событиям в Москве, Петербурге, Тбилиси, Ереване, Белграде, Стамбуле и других городах. Читайте наши репортажи, расследования и эксклюзивные свидетельства. Мир — есть все, что имеет место. Мы остаемся в нем с вами.